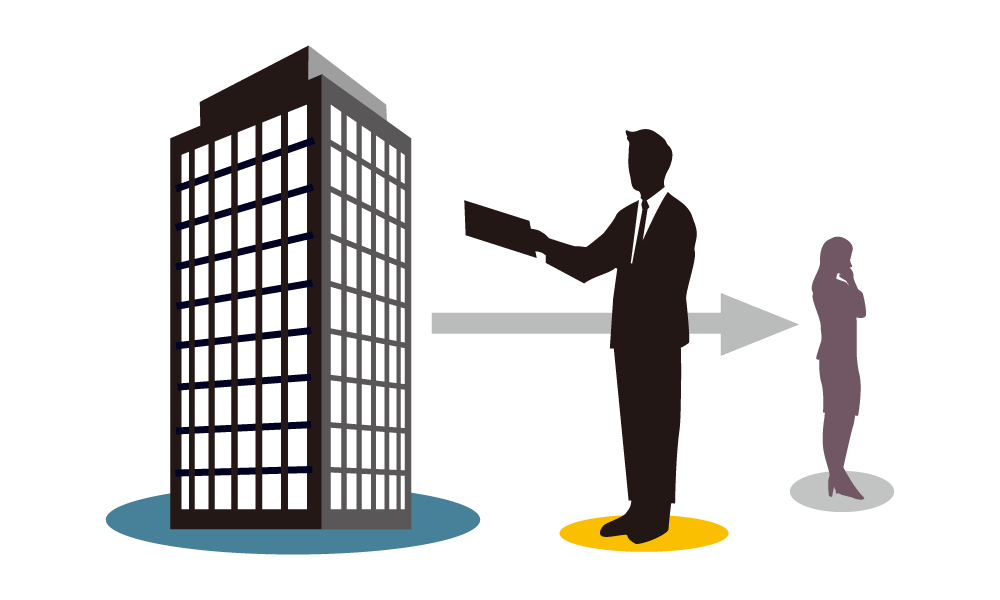
令和の新ビジネス慣行!「退職代行を使った退職」にどう対処する?
■急増する退職代行を使った退職 「退職代行」を使った退職が……
■急増する退職代行を使った退職 「退職代行」を使った退職が……
人間の能力を測る指標にはさまざまなものがある。代表的なものがIQ=Intel……
トランプ米国大統領の言動に揺れる国際社会。終わらないウクライナ戦争とイスラエ……
長引く円安や国際情勢不安により日本人の海外渡航が難しい状況だが、インバウンド……
「気づき力」は、単に感覚的に「鋭くなる」ことではない。目に見えないものに目を……
ビジネスの現場では、目に見える成果が評価される。しかし、その成否を分けている……
AIやDXが進展し、予測技術が日々精度を高めていく中、企業では社員の「失敗す……
■新型コロナパンデミックで、会社と社員の絆が弱まる あなた……
■右肩上がりの男性化粧品・ボディケア市場 男性化粧品という……
「社内政治力」という言葉が注目を集めている。社内政治力というとどんなイメージ……
■「もふもふ」は、最初食パンを食べる擬音だった 気がつくと……
昨年のクリスマス、日本を代表する自動車・二輪メーカーのスズキのトップを長年務……